Climate protection, environmental awareness, sustainability – these issues concern us all.
How can I avoid the waste of raw materials?
How can I ensure transparency from the procurement of raw materials all the way to the finished product?
Can our company reduce greenhouse gas emissions?
How can I make sustainability an integral part of our corporate philosophy?
That’s why at Hydewa, we are continuously striving for improvements in product management and always looking for new approaches in this regard.
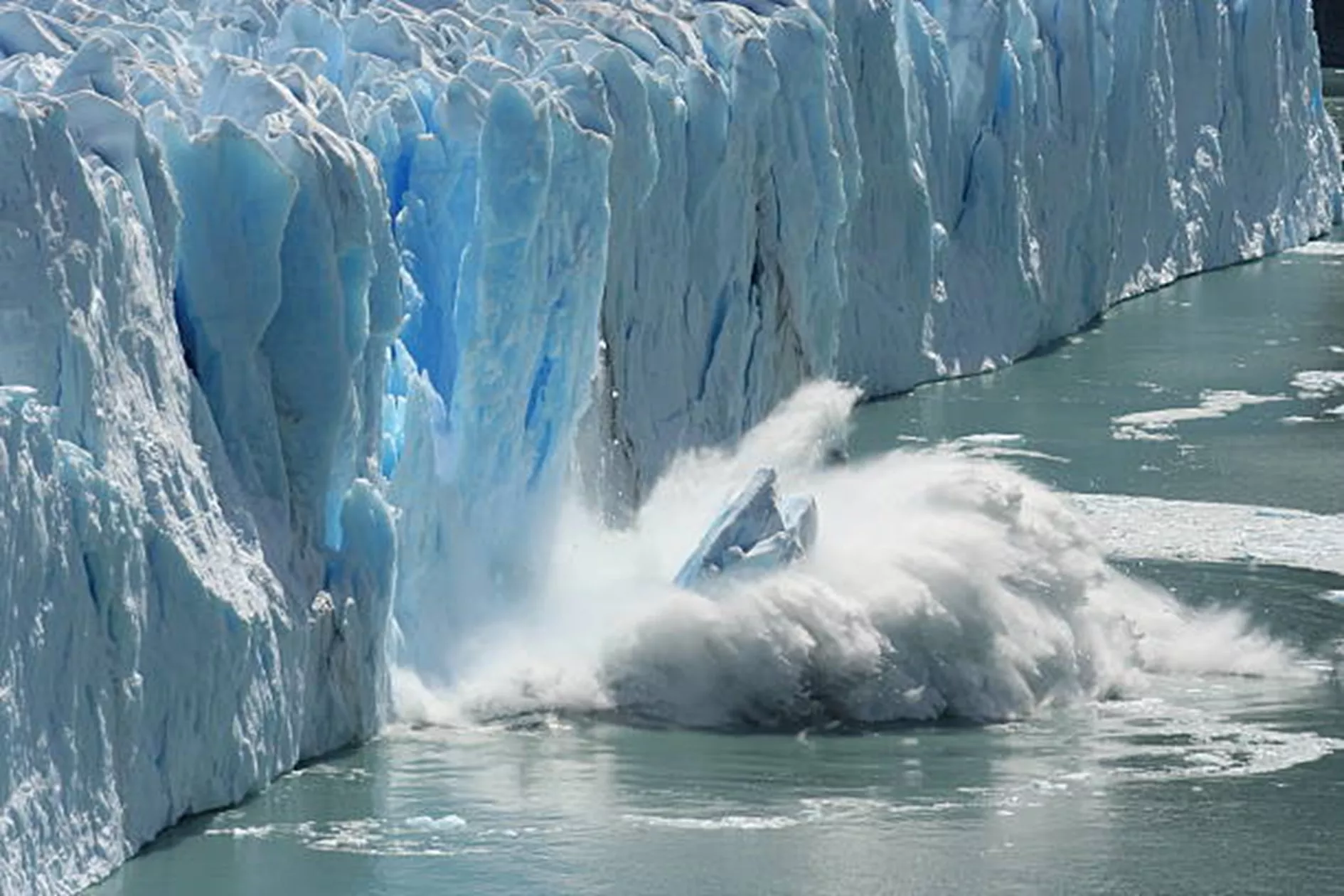
All of these questions have been central to our efforts at Hydewa as we strive to play our part in advancing sustainability.
This commitment begins with the sourcing of raw materials. Since we import our core product, Glasbord®, from the United States, careful planning is essential to avoid unnecessarily frequent transport routes.
We also apply sustainable thinking when selecting our suppliers.
For example, in the lamination of our sandwich panels, we use ROMA5 BMB foam systems for the insulation core. These systems already replace fossil raw materials with biomass—such as organic kitchen waste—during the production process.
Our supplier ROMA thus provides us with a resource-efficient PU foam system that can reduce CO₂ emissions by up to 50% during production.
Another supplier, Kingspan / EMS, holds a “Certificate of Approval” under the BES 6001 standard for responsible sourcing. This certification covers and evaluates areas such as resource consumption, greenhouse gas emissions, energy management, waste reduction and management, material traceability, ecotoxicity, and much more.
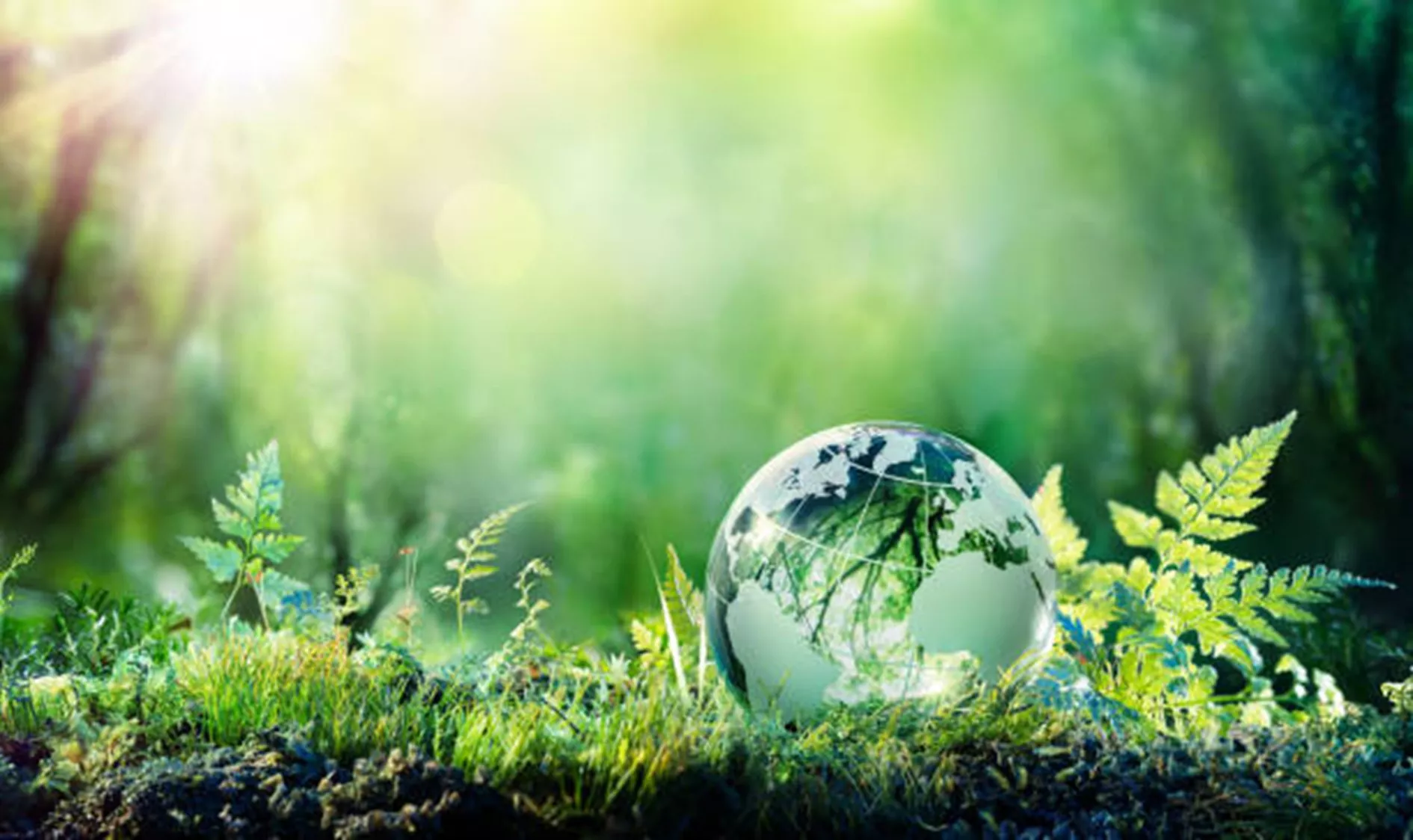
Packaging
Packaging plays a vital role in protecting and transporting our products. At the same time, however, it also contributes to environmental pollution. This makes it all the more important that our packaging materials are either recyclable or made from recycled materials—and that they are used as sparingly as possible.
We use film packaging that contains at least 25% environmentally friendly post-consumer recycled material (PCR) in accordance with DIN EN 14021, which can be returned to the recycling process after use.
This ties into our broader sustainability goals, particularly in production, where our top priority is to avoid generating waste wherever possible. When waste does occur, we separate and recycle it to the greatest extent possible.
Key focus areas include reducing production errors and reusing B-grade materials.
Thanks to our quality management system and ongoing process improvements, the volume of B-grade products remains very low.
Nevertheless, any B-grade material that does arise is structurally sound but may have cosmetic imperfections that do not meet customer specifications.
We now reuse such material internally for renovation and refurbishment projects, and we also offer it to others—e.g., as dust protection walls for construction sites—at cost price for pickup.
Each reused panel or sandwich element is one less item headed to landfill. And our internal renovation projects help improve working conditions for our employees in a cost-effective way.
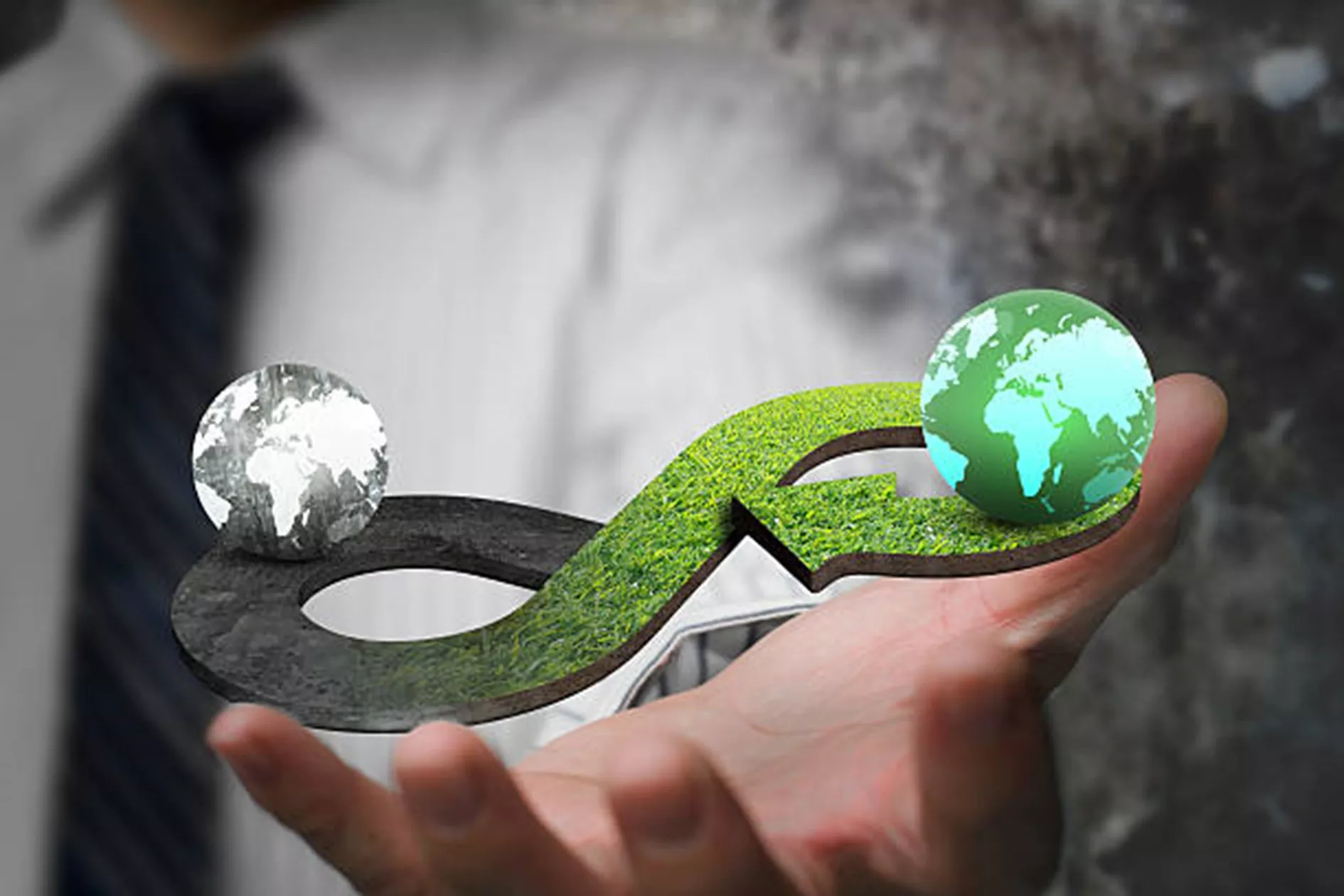
Waste
Our goal is to keep waste out of landfills and to continuously increase the proportion of materials being successfully recycled within our current recycling streams.
Our recycling programs target specific materials such as metals, wood, plastics, chemicals, and packaging materials.
All other waste materials—such as fiberglass (FRP), Styrofoam, and certain plastics—that cannot be fully recycled as raw materials are collected in a 50 m³ roll-off container in cooperation with our selected long-term waste disposal partner and processed into alternative fuel for the cement industry.
This disposal company maintains fixed volume quotas and contracts with cement plants, which is only possible due to the delivery of high-quality, closely monitored waste materials.
Styrofoam milling residues and GRP dust are compressed, collected in so-called "Big Packs," and picked up by the local waste disposal company.
Styrofoam waste generated at the beginning and end of production or during coil changes is returned to the supplier and reintegrated into the material cycle.
Another important environmental aspect of our approach is the use of a local waste disposal partner. This not only ensures short transport distances but also supports regional cement plants exclusively.
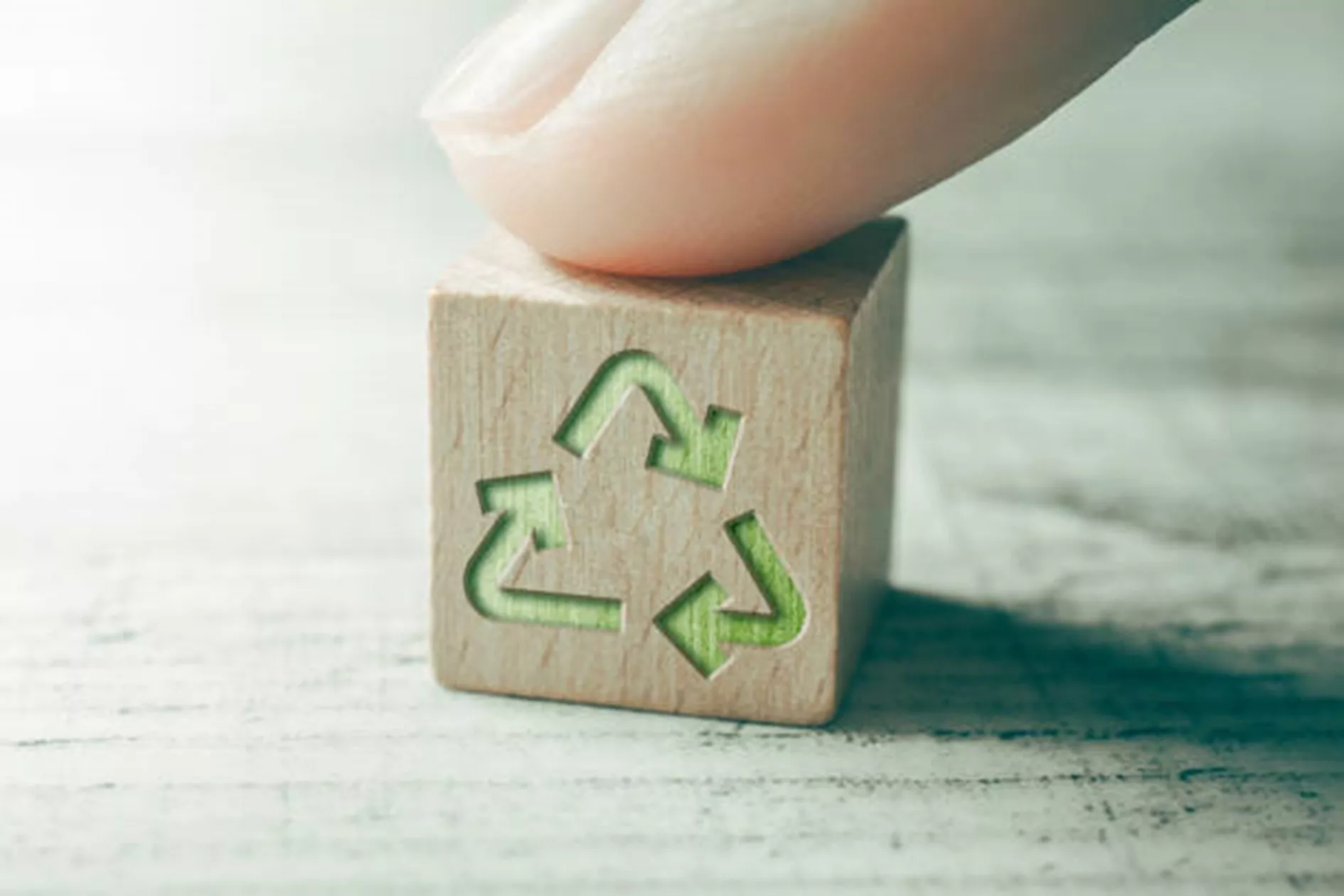
Energy and Climate
Ultimately, we need energy to manufacture our products. This raises important questions: How much energy do we use—and where does it come from?
When it comes to energy sources, we rely on photovoltaic systems and renewable energy. For example, we provide our employees with electric vehicles and charging stations on our company premises.
To improve our energy footprint, we have equipped our office building with LED lighting, which stands out due to its long lifespan, low energy consumption, and minimal heat generation.
Another contribution to environmental protection is the infrared heating system installed in our warehouse.
The result: up to 70% energy savings and significantly reduced CO₂ emissions.
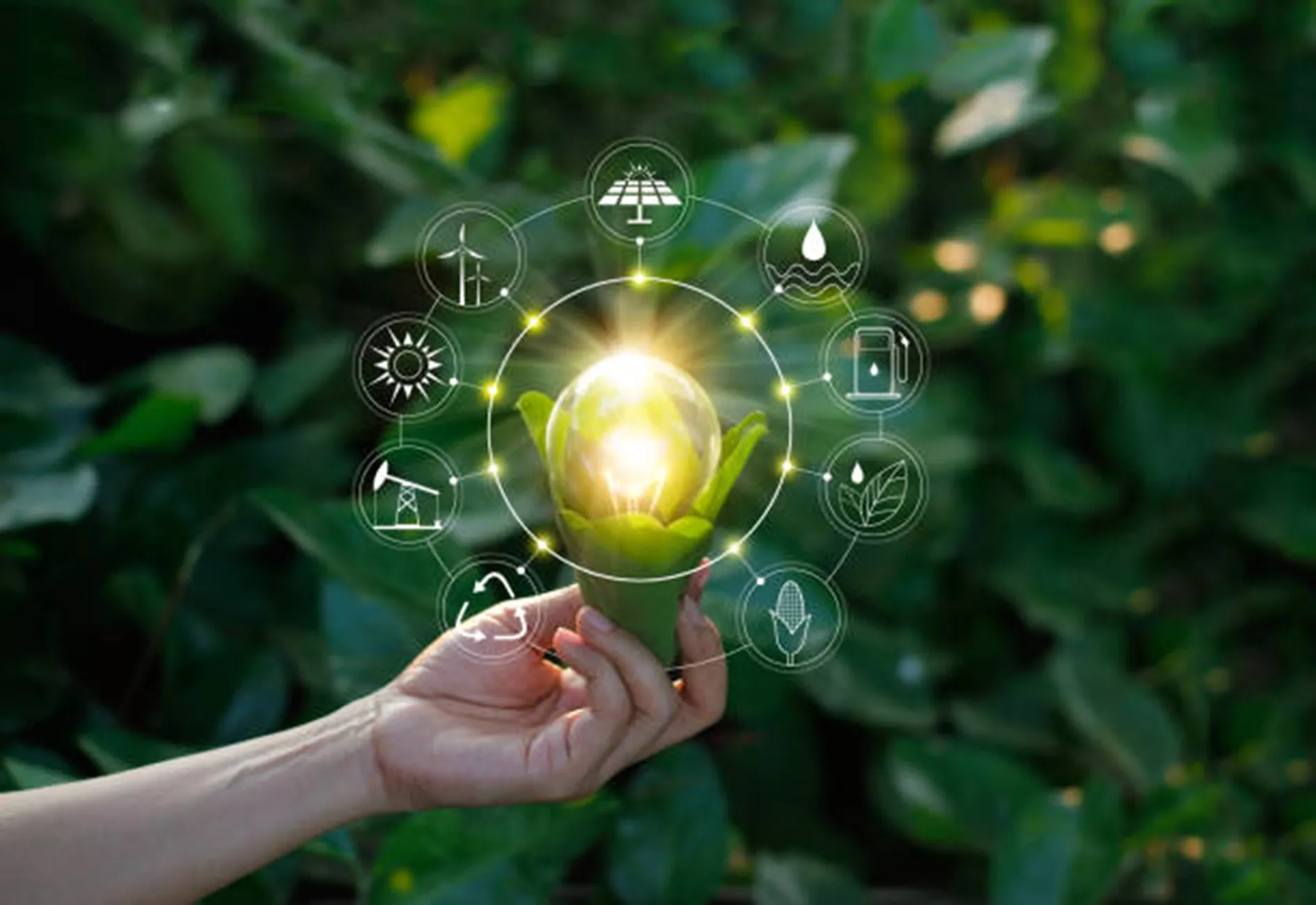
Responsibility as an Employer
As a responsible employer, we rely on skilled and dedicated employees—and we actively raise awareness about environmental issues within our workforce.
And what could be better than training future professionals ourselves? We offer apprenticeships with real long-term prospects in a supportive, family-like team environment.
Sustainability is a team effort—it doesn't depend solely on those in leadership roles.
Only by working together can we pursue our goals and continue to improve every day.
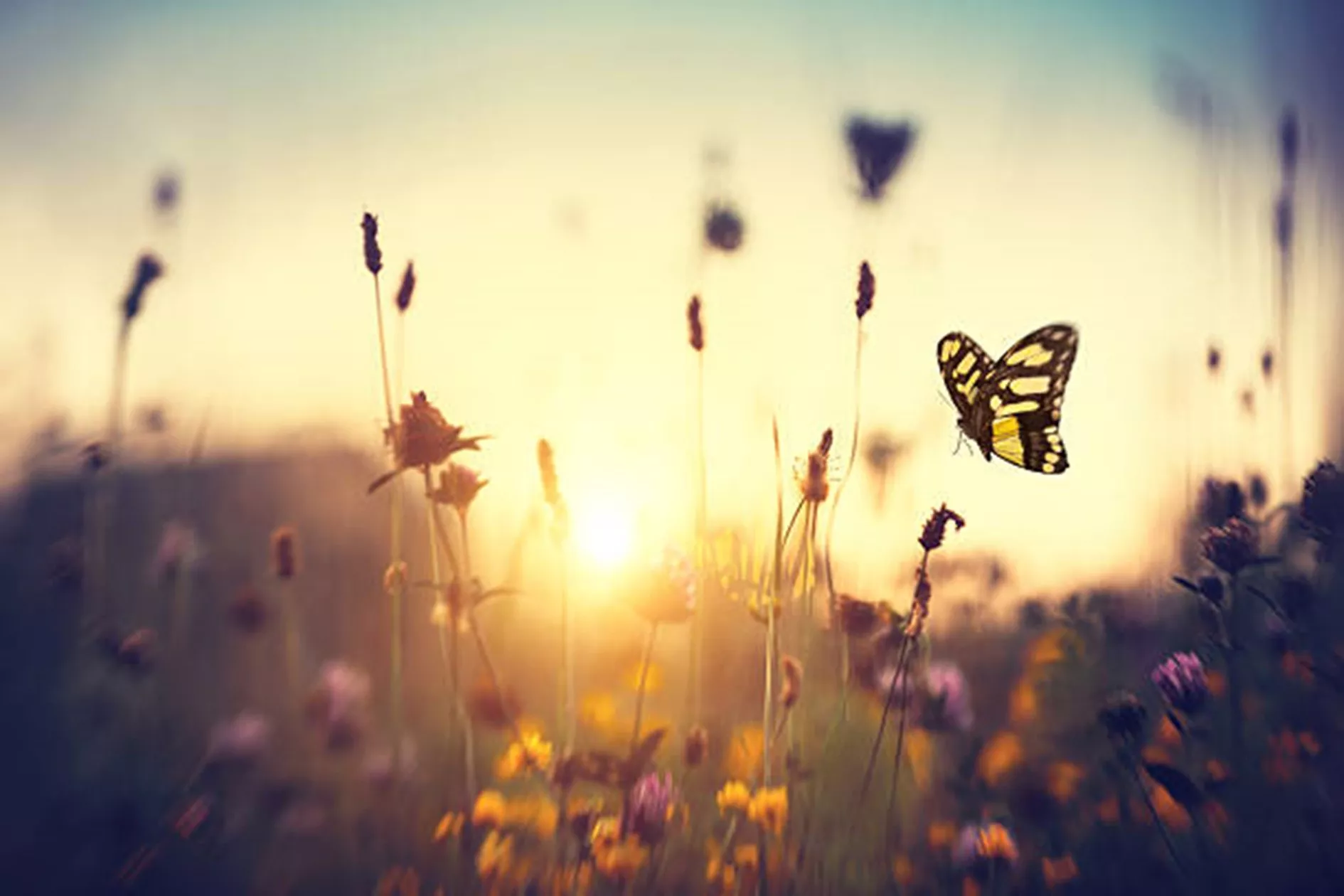